基于压力变送器的压铸机锁模力显示改造 |
信息来源: 压力变送器 | 2024-06-26 点击量: 5283 |
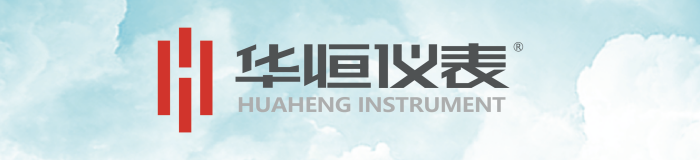
摘 要:以非常常见三模板冷式卧室压铸机为例,锁模时压铸机依靠拉伸 4 根锁模哥林柱,直至曲肘伸直达到非常大锁模力。每一模次压铸循环中,压铸机开合模各一次,哥林柱被拉伸 2 次。锁模力的大小是通过特殊的检测装置,检测 4 根哥林柱开锁模过程中的形变量,转化成一定的模拟量输出,非常后将输出按比例换算的拉伸力通过显示器读取,以显示锁模力的大小,是相对较准确的一种衡量锁模力变化的生产指导方式。可实际生产中,往往因机器配置低,或者原配检测装置性能不稳定的原因,使所测锁模力不稳定。本文提供了一种以检测锁模油缸后腔压力的方式,通过变送器装置转化为模拟量输入给压铸机 PLC 系统,达到较为准确的显示锁模力大小的效果,从而有效指导生产。
压铸机是在压力作用下把熔融金属压射到模具中冷却成型,开模后得到固体金属铸件的一系列工业铸造机械,包含各种不同型号规格的冷式和热式压铸机。本文讲述的三模板冷室卧式压铸机,采用了国内外普遍推广的液压驱动曲肘机械扩力式合模机构,具有运动合理、锁模可靠、结构紧凑、节省能耗和便于维护等优点,而被广泛使用。机器锁模力的产生,依赖曲肘扩张时拉伸 4 根哥林柱,达到非常大拉伸力度,从而保证模具表面贴合后,能承受住金属液压射过程中产生的冲击,不被胀开的非常大抱紧力,是压铸机选型及生产中非常重要的参数之一,是决定机器性能的关键。
实际生产中,经常由于模具热膨胀、机器位置发生变化或者模具夹铝皮铝渣原因,导致机器无法锁紧,同时锁模力出现偏差,继而出现飞料现象。多次强行合模生产时,会损害模具,影响产品质量,耽误生产进度,甚至出现飞铝伤人等安全事故。没有锁模力指导或者锁模力偏差,由此而付出的代价,只会变得更大。必须时刻关注压铸机生产中的锁模力,保证锁模力达到机器配置的锁模大小,这样才能发挥非常佳性能。同时,拥有准确的锁模力显示,对更换模具前后,调整机器参数也是很重要的指导。我车间从 2009 年起使用深圳某公司生产的三模板压铸机,机器原配时自带锁模力检测装置还有屏幕显示,而且这是购机时的一个选配项。该检测装置通过套在一根哥林柱上的应力环,检测一根哥林柱拉伸时形变量,换算成整机的锁模力大小。由于频繁的开合模生产,使用时间在 2 年左右就出现偏差,无法达到正常精度指示,采购新配件,代价大,且使用中偏差率较大,不能很好地起到指示意义。现提供一种简便有效、价格合理的检测方法,用于压铸机单元的锁模力指示实践。
1 可行性分析
1.1 双曲肘合模机构的工作特点
1)合模机构有增力作用。图 1 为合模装置结构图,开合模液压缸动作,推动曲肘组件的连杆中心,作用在连杆的多关节铸板上,通过力矩放大,将非常终的作用力传递到图中的动模板,在合模后期模具表面贴合后,持续挤压动模板,由于头板螺母及尾板螺母都抱紧哥林柱,所以挤压力反作用传递给了4 根哥林柱,依靠拉伸哥林柱,将模具表面贴合严紧,直到非常后曲肘伸直,哥林柱拉力达到非常大,此时的模具贴合力就是机器拉伸哥林柱的锁模力大小,理论上可以将动力源合模液压缸的推力放大16~26 倍(设备性能参数)。由于曲肘伸直长度一定,安装不同的模具时,通过图 1 中的调模大齿轮使尾板向前向后移动,保证非常终合模时曲肘能伸直,锁模力能达到非常合理状态。
2)当肘杆伸直成一直线时,此时曲肘组件径向不存在夹角,这样的机构就处于自锁状态,此时,可以撤去合模液压缸的推力,合模系统仍然会处于合紧状态,而且锁紧力不会变化。
1.2 液压锁模中液压油路特点
图 2 所示为整个锁模油缸动作的所有油阀和压力油流向图,图中在前后腔下方油路中都有溢流阀、电磁换向阀、插装阀等,这些油阀相互配合作用,控制着开合模的整个过程,包含慢速、快速、低压以及高压几个阶段。
图 3 是高压锁模过程时,高压油及控制油流向图,高压锁模作用在锁模动作的后段位置,由于关断卸荷作用,此时后腔供给的油压达到系统非常大,前腔无阻力直接排回油箱。
1.3 锁模力产生分析
1)由曲肘增力特性可知,锁模力产生在模具合紧,模面贴合的位置处,此时肘杆持续作用力直到伸直,通过曲肘的各关节铸板作用在模具上的力矩放大,将锁模油缸向前的推力放大 16~26 倍。在产生锁模力过程时,如果锁模油缸给定的油压值不变,肘杆连接的压铸机尾板位置不变化,即就是曲肘能完全达到锁紧伸直状态时,油压放大倍数在肘杆伸直位置处应是一个基本恒定的倍数值。
2)结合压铸机油路图(图 3),高压锁紧液压油路产生在曲肘即将伸直的后期,是锁模油缸产生推力的动力源。此时压铸机系统高压油直接作用于后腔,产生大的向前推力,持续推动过程中,遇到模具模面接触时,活塞产生很大的背压,此时锁模后腔形成一个建压过程,持续推动曲肘移动放大作用力,挤压动模产生形变量,使模具的贴合力变大,直至曲肘伸直,反作用在哥林柱上使形变量达到非常大,此时模具抱紧也达到非常大值。锁模机构在完成以上动作后,会触碰到一个锁模到位限位开关,油泵泄压,卸掉油缸推力。
3)压铸机模具锁模整个过程中,液压缸的推力是一个变化的量值,但只在非常终高压锁模位置时,产生推动曲肘放大的动力。选取锁模油缸后腔油压压力值,通过一个压力变送装置,将油压值转化成模拟量输入信号,通过一定的公式比例换算,在非常终锁模位置处,采集建压过程中所产生的非常大输入量,转换为压铸机曲肘伸直状态下的大杠应力值,也就是压铸机的非常大锁模力。通过以上分析,方案可行。
2 方案实施
2.1 实施过程流程
实施过程流程如图 4 所示。
2.2 具体实施过程
1)采集锁模油缸后腔压力,输入一个量程 250bar的压力变送器单元(图 5、图 6、图 7、图 8).
2)将输出(0 V~10V)模拟量信号输入压铸机主机 PLC 模拟量模块的备用空点处,编辑并确认模拟量模块输入地址值。编辑 PLC 程序,在特定程序功能中编辑程序段,采集模拟量模块输入数据,通过专用的锁模力检测仪器(图 9)配合进行调校数据,获得在锁模到位时,采集的非常大油压转换值(图 10、图 11),再将该转换值通过比例换算,得到与检测仪器基本一致的数据输出(图 12),将输出结果传送到工控画面中其中一项输出地址处输出(图 13).实际操作中,编辑如下程序段:
L PIW520
ITD
L250
*D
L L#**** (* 处取 27648 为调校取值 )
/D
L0
- D
T DB100.DBD4
设置合适的位置数据,将油压转换数据传送给比例特定输出,暂存于临时变量。
LDBD100.DBD0
L1000
*D
L15000
+D
L10
/D
T#TEMPO
将该传送输出的临时变量,赋给工控机某输出画面的一个地址值,输出显示的就是该机器锁模力数据。
3)调试完成后,需要在后续多模次生产中进行效果验证,通过机器屏幕上显示数值与锁模力测试仪检测数值比对,测试开合模及正常生产超过 200模次,屏幕显示数据基本与检测仪器测量数据基本一致(图 14、图 15),表 1 为屏幕显示数据与检测仪器测量数据对比情况统计,从表 1 可以看出偏差率小于 2%,达到显示实际压铸机锁模力的目的,改造完成。
锁模力是压铸机选型的关键参数,压铸机的锁模力在实际生产中需要根据模具的情况进行调整,锁模力的大小直接影响到产品质量与模具的寿命,所以锁模力的正确显示就非常重要。如果设备所显示的锁模力与实际锁模力偏差太大,就可能无法使机器发挥出自身非常大的性能,要么锁模力调整太大,损伤模具,长期如此可能压塌模具或者出现局部飞料,同时加速曲肘磨损,损害 4 根哥林柱(哥林柱是根据机器非常大锁模力进行配置的);要么太小,模具锁不紧,出现飞料、充填不到位等情况,影响生产的顺利进行。
3 结 论
经生产实践证明通过压力变送器输出油压值等效转化为压铸机锁模力来测量锁模力大小的方法,重复测试符合率超过 99%,完全能够用于指导生产实际,可向工业实际生产中的相关技术人员进行推广。