利用压力变送器进行循环流化床炉膛颗粒浓度分布和循环流率实验研究 |
信息来源: 压力变送器 | 2021-12-31 点击量: 5224 |
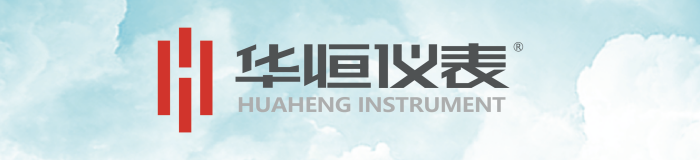
摘要:在高度为10m循环流化床冷态试验台上,采用差压法和积料法分别测定流化床炉膛颗粒浓度分布和物料循环流率,研究不同颗粒物料、在不同气流速度炉内颗粒浓度分布特性和循环流率规律。研究表明循环流化床颗粒浓度沿炉膛高度方向呈现先急剧降低后缓慢减小的规律。对于一定的颗粒物料,炉膛气流速度(截面速度)决定了炉膛稀相区区域物料浓度和和循环流化床锅炉的固体物料循环流率。
人类大规模利用化石能源排放大量的温室气体被普遍认为是导致全球变暖的重要因素。我国的能源消费结构以煤为主,其中燃煤发电消耗煤量巨大,燃煤产生巨量的CO2排放。目前CO2的减排措施,一方面是通过提高煤炭利用效率达到少用煤减少CO2排放目的,另一方面,对燃煤产生的CO2进行捕集,如富氧燃烧,烟气中CO2分离,然后对高浓度的CO2进行压缩、输送、地下封存。然而,不管是采用富氧燃烧还是烟气中CO2分离措施,能耗均非常大,大规模应用几乎不能接受,因此,近年来在CO2捕集方面具有显著低能耗优势的化学链燃烧技术的研究进程明显加速。
化学链燃烧是一种洁净、高效新型无火焰燃烧技术。与传统燃烧相比,该技术的非常大优点是借助于中间载体在氧化-还原反应器间的循环,避免了燃料与空气直接接触,在化学转化同时实现CO2高效分离,在降低CO2捕集能耗方面具有优势。化学链燃烧工艺包括空气反应器和燃料反应器,双流化床反应器被认为是化学链燃烧非常合适的反应器,其反应器中的燃料或载氧体流动状态与循环流化床锅炉炉膛内的固体颗粒的流动、循环类似。循环流化床锅炉燃烧技术以燃烧效率高、环保特性好、调峰性能好、燃料适应性强等优点在电力行业获得广泛应用,技术已很成熟,为化学链燃烧技术发展奠定了良好基础。
化学链燃烧的概念首先由德国科学家Richter1983年提出,用来替代传统燃烧提高火电厂热效率;1987年日本学者Ishida与中国金红光指出CLC具有CO2内分离的特性,并进行了实验研究与理论分析,2004年瑞典学者Lyngfelt等人实现了串行流化床化学链燃烧中试实验,证明了化学链燃烧可以实现CO2内分离。清华大学、东南大学、华中科技大学和华北电力大学在载氧体开发与测试以及小型试验装置运行方面进行相关研究。化学链燃烧动力系统已成为世界能源领域研究的重要方向,是解决CO2减排的主要发展的先进技术之一[1]。
化学链燃烧/气化技术应用了流化床技术,采用载氧体循环物料的化学链燃烧/气化技术,炉膛颗粒浓度分布和循环流率等关键参数直接影响到炉内的气固流动、燃烧/气化反应、传热特性、磨损和产物生成特性,也是关系到化学链技术能够实现工业化应用的关键所在[2-4]。本文在东方电气东方锅炉股份有限公司德阳基地试验中心,采用炉膛内截面为400mm400mm,炉膛高度(距离布风板)为10m循环流化床试验台,以钛铁矿和循环灰为床料开展不同物料特性对流化床内颗粒浓度分布和物料循环流率影响规律试验研究,为化学链燃烧/气化技术工程化应用提供重要的技术支撑。
1实验装置及方法
流化床冷态实验系统主要包括炉膛、分离器、下降管、返料器、供风系统、引风系统、压力采集系统、风量测量系统等。炉膛高度(距离布风板)为10m,布风板截面为280mm400mm,下炉膛变截面段高度为900mm,上部炉膛内截面为400mm400mm,下降管内圆直径为120mm。为了保证流化床内部气固流动的可视化,试验部件均采用有机玻璃制成。实验台沿炉膛高度布置有10个压力测点,旋风分离器出口和入口均布置1个压力测点,下降管上布置有4个压力测点,返料器上布置有4个压力测点,返料腿上设置1个压力测点,在炉膛一次风室、返料器的流化风室和返料风室分别布置1个压力测点。采用压力变送器实时采集实验台各点的压力值,利用压差浓度法P=P/(gh炉膛)计算炉膛沿高度方向的颗粒浓度,其中P为炉膛颗粒浓度kg/m3;P为相邻两侧点压力差Pa;g为重力加速度m/s2;h炉膛相邻两侧点高度差m。试验过程中,由于流化床内物料湍流流动状态极其强烈,炉膛内压力值波动较大,测量压力数据为稳定工况下,一分钟内压力测量数据的算术平均值。物料循环流率采用积料法测量,在实验台返料器上设置有回料截止阀,在系统稳定运行的瞬间截止回料,并测量物料在下降管的堆积速度,通过计算公式Gs=bh下降管S下降管/(TsS炉膛)计算循环流率,其中Gs为基于炉膛内截面积的物料循环流率kg/(m2s);b为物料颗粒的堆积密度kg/m3h下降管为下降管的堆积高度m;S下降管为下降管的内截面积m2;S炉膛为炉膛的内截面积m2;为物料颗粒堆积时间s。
试验物料采用钛铁矿和循环流化床锅炉实际运行的循环灰,通过称量测出其堆积密度分别为2620kg/m3、1200kg/m3。采用筛分装置对钛铁矿和循环灰分别进行粒径筛分(见图1~2所示),结果表明,钛铁矿粒径范围为0m~300m,D50中位粒径约为160m,循环灰粒径范围是0m~300m,D50中位粒径为110m,且均符合玻尔兹曼分布规律Y=A2+(A1-A2)/(1+EXP((X-X0)/DX))(BoltzmannModel)。本次整个试验在常温常压下进行,流化介质为空气。
2实验结果与讨论
2.1循环流化床试验台压力分布
本次试验分别采用钛铁矿和CFB锅炉循环灰为床料,采用压力传感器和数据采集系统实时采集压力变化。试验在炉膛空截面速度3.6m/s下,采用钛铁矿(静止床料厚度310mm,床料量97.5kg)和CFB锅炉循环灰(静止床料厚度490mm,床料量60kg)的压力分布趋势如图3和图4所示。
试验结果表明,采用合适粒径分布的钛铁矿为物料,能够实现在循环流化床冷态试验台的正常运行,且炉膛内压力分布趋势与采用循环灰为物料的运行状况规律一致。从压力分布曲线可看出,钛铁矿比CFB锅炉循环灰堆积密度大得多,其单位堆积厚度的床压降比CFB锅炉循环灰高,在流化状态下,运行床压与床料密度和堆积厚度有关。
2.2截面速度对炉膛颗粒浓度的影响
图5给出采用钛铁矿试验床料,静止炉膛高度为310mm(即床料量58.2kg),不同截面速度下沿炉膛高度方向钛铁矿颗粒的浓度分布趋势图,整体而言,炉膛颗粒浓度沿炉膛高度方向均呈现逐渐降低的趋势,且颗粒浓度在h/H=0.045以下的炉膛区域急剧下降,在h/H=0.045以上的炉膛区域缓慢下降,其中h为炉膛压力测点高度,H为炉膛总高度;
在试验截面速度范围内(2.5m/s3.6m/s),炉膛密相区(h=0~3500mm)和稀相区(h=3500mm~10000mm)压降与截面速度的关系曲线见图6,由曲线可知随着截面速度增加炉膛密相区的压差呈现下降趋势(5800Pa5035Pa),炉膛稀相区差压值呈现上升趋势(122Pa715Pa),表明,随着截面速度升高,炉膛密相区床料充气膨胀更强烈,气/固比升高,而稀相区压差随截面速度的升高而升高,说明气体对钛铁矿颗粒的携带能力增强。
2.3截面速度对循环流率的影响
图7给出采用钛铁矿为试验床料,静止炉膛高度分别为190mm、400mm、470mm(即对应床料量分别58.2kg、128.3kg、153.2kg),不同截面速度与循环速率的趋势图。由图可知,对不同床料量钛铁矿而言,随着炉膛截面流速的升高,单位炉膛截面的循环流率增大。图8给出采用600MW超临界CFB锅炉燃煤机组的循环灰为试验床料,静止炉膛高度分别为295mm、410mm、490mm(即对应床料量分别27.3kg、45.7kg、60.0kg),不同截面速度与循环速率的趋势图。由图可知,不同静止炉膛高度的循环灰循环流率与炉膛截面速度均呈现线性关系。
2.4炉膛差压与循环流率的关系
对循环流化床锅炉,工程上通常采用炉膛差压值间接反映锅炉循环速率大小。由图9可知针对钛铁矿床料而言,在稀相区高度段(即H3=3500mm~9760mm)炉膛差压与循环流率的一元线性相关系数r=0.96,呈现线性关系。对循环灰床料而言,稀相区高度段(即H3=3500mm~9760mm)炉膛差压与循环流率的一元线性相关系数r=0.91,呈现线性关系。整体趋势上看,循环灰的炉膛差压与循环流率一元线性关系与采用钛铁矿类似,且两者一元线性的斜率和相关系数r存在一定差异,造成上述差异原因与床料颗粒从分离器出口物料损失速率、床料颗粒在炉膛内的气/固比等因素差异有关(注:分离器出口几乎没有钛铁矿颗粒物料损失,而循环灰颗粒有不同程度物料损失)。
2.6不同物料颗粒对循环流率的影响
本文采用物料粒径范围为0m~300m钛铁矿(D50=160m,b=2620kg/m3)和循环灰(D50=110m,b=1200kg/m3)床料开展冷态试验研究,图10给出了不同物性床料颗粒的炉膛静止床料质量与循环流率关系图。由图可知,炉膛静止床料质量约60kg,炉膛截面风速为2.8m/s时,循环灰颗粒循环流率为11.09kg/(sm2)明显高于钛铁矿颗粒的循环流率2.70kg/(sm2);炉膛截面风速为3.6m/s时,循环灰颗粒循环流率为17.40kg/(sm2)明显高于钛铁矿颗粒的循环流率4.92kg/(sm2),即循环灰的循环流率明显高于钛铁矿的循环流率。导致该现象的主要原因是两种床料颗粒密度、粒径分布和物性参数等存在差异,钛铁矿真实密度P=5000kg/m3,堆积密度b=2620kg/m3,D50=160m,循环灰真实密度P=2500kg/m3,堆积密度b=1200kg/m3,D50=110m,非常终造成两种床料颗粒的流化特性(相同物料量和流化速度)存在一定程度的差异。
3结语
由上述分析计算可得能下结论。
(1)采用合适粒径分布的钛铁矿为物料,能够实现在循环流化床冷态试验台的正常运行,且炉膛内压力分布趋势与采用循环灰为物料的运行状况规律一致。
(2)本次试验的钛铁矿颗粒浓度沿炉膛高度方向均呈现逐渐降低趋势,颗粒浓度在h/H=0.045以下炉膛区域急剧下降,在h/H=0.045以上炉膛区域缓慢下降,其中h为炉膛压力测点高度,H为炉膛总高度。试验表明,随着截面速度升高,气体对钛铁矿颗粒的携带能力逐渐增强,且密相区和稀相区的中间位置约为h=3500mm(即h/H=0.35)。
(3)本次试验钛铁矿和循环灰两种颗粒均随着炉膛截面流速的升高,单位炉膛截面的循环流率增大;在相同物料量和流化速度下,循环灰的循环流率明显高于钛铁矿的循环流率。
(4)鉴于本次试验条件下的钛铁矿颗粒的循环流率偏低,可能会影响到热态试验台炉内传热和温度场分布,因此实际化学链反应器设计时还需要进一步优化钛铁矿粒径分布、静止床层物料高度(床内存料量)、选择合适运行速度(炉膛截面速度),以及考虑有效防磨措施。